Q. What’s the secret to turning your complex designs into a product reality?
A. It’s pretty simple really – a fold line!
Q. What’s a chemically etched or milled fold line and why is it so important?
A. The fold line is where a line is chemically etched into the metal about halfway through to give a U profile. Which controls the position of a fold, as the metal bends at its weakest point. 90° bends are achieved when both edges of the U profile touch. A wider fold line will allow 180° folds – right over, there is no measurable internal radius. The external radius is half of the metal thickness. Dimensions can be controlled to ±0.1mm. Some quite complex shapes can be made by having fold lines on both sides.
Part No. 37999A is made from µ metal – an iron alloy that has desirable RF magnetic shielding properties, however, it is particularly difficult to cut and work – it does not want to go! This was solved by etching the blank (one atom at a time) and fold lines. Chemical milling allowed the fold line to be worked into the required shape and accurate radiuses were obtained. Conventional metal working guillotine and folding would not have worked at all on this part. The added benefit of the chemical milling process is rounded edges with no burrs.
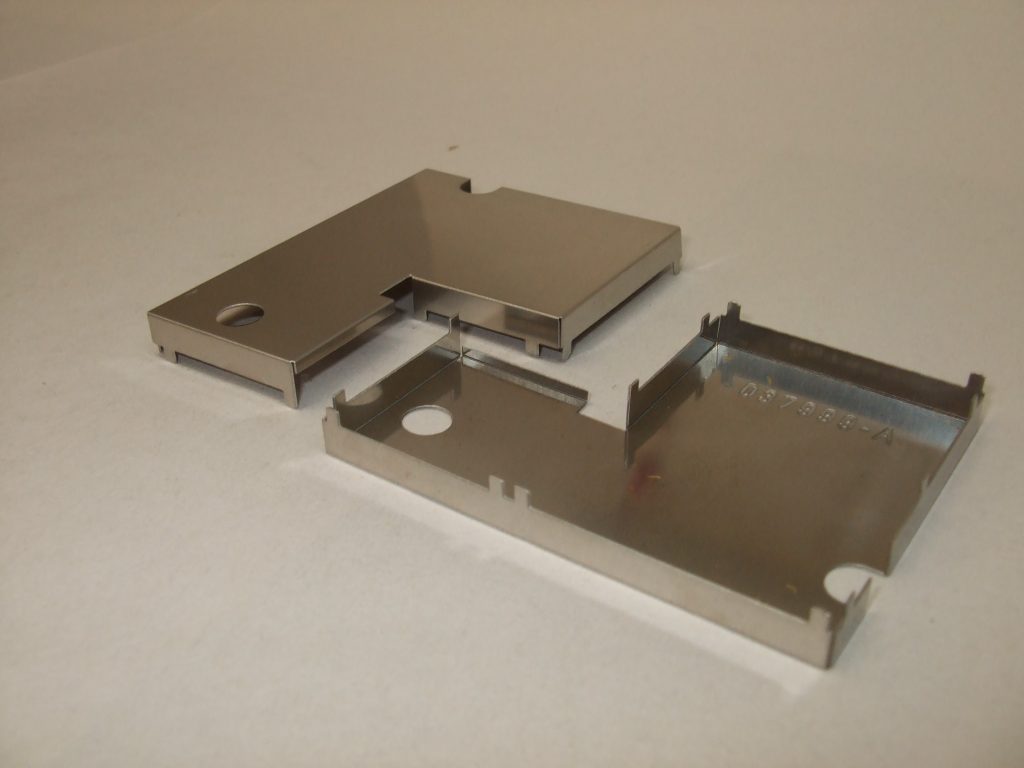
If it is necessary to change the position of a fold line it can simply done on the film work in a very short time.
One of the shields below has 10 successive folds in a row and the final dimensional accuracy have been achieved.
Other applications of the half etch principle which make your parts unique are;
- part numbers,
- QR codes,
- barcodes
- text can be etched to identify the parts thus saving labelling costs.
With a ¾ etch, provision can be made for tear-off and removable sections.
While they are in flat panels, parts can be electroplated before fabrication, thus allowing a uniform thickness and appearance.
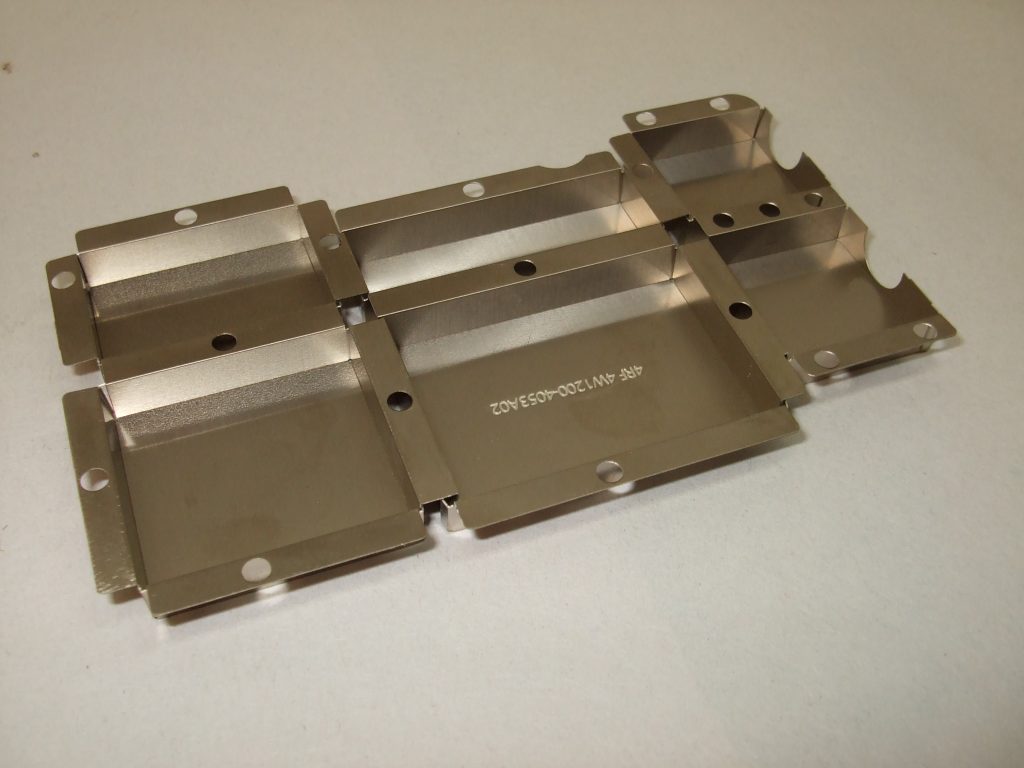
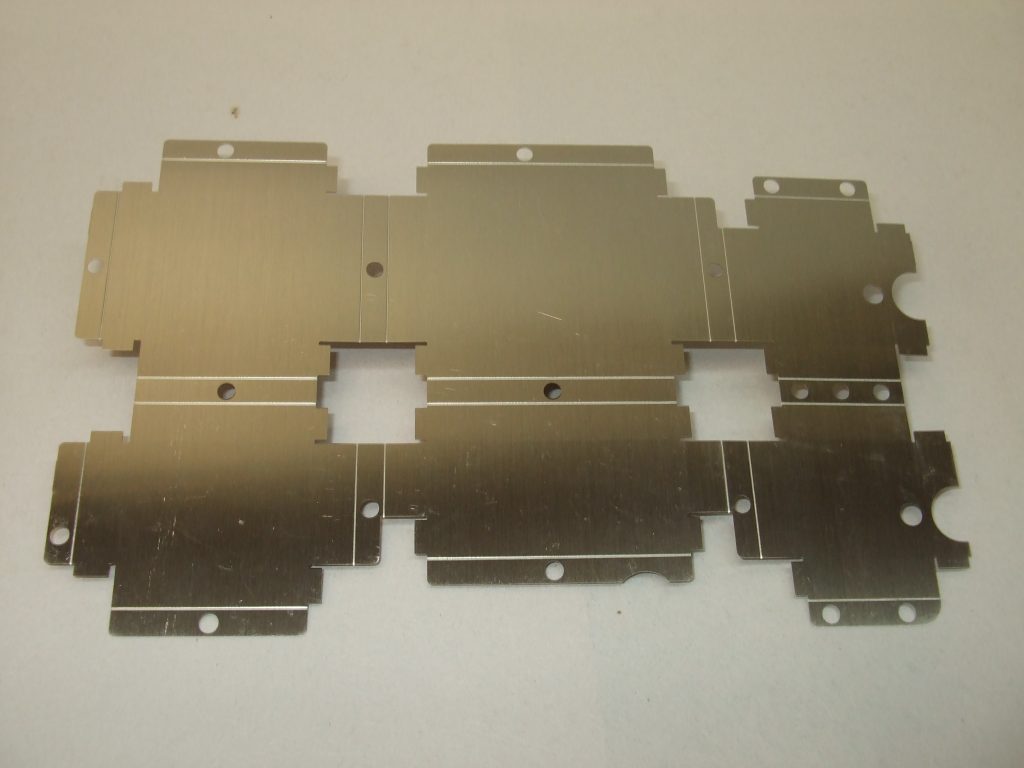